I wanted to powdercoat the rims of my wheels to match the "aluminum blast" that I put on the motor, so went and got my spare wheels from the shed. My buddy Panhead Pat is going to help me break down the spoke and teach me to re-lace. To my surprise they still had tires on them. I forgot about that. The sad thing is that the tires on my spare rims were a little nicer than ones on my bike now.

So this is how I take my tires off. Take the valve core off.

Take the lock nut off the valve stem.

Time to break the bead. Now this the part I'm proud of. I designed and build this bead breaker myself. I based it off the two internet ideas I saw. One used a huge lever and wedge attached to a wall stud and the other used a big hydraulic press from Harbor Freight. Both of those options were too big to mess with and use one a year or so on tires. So here it is.

Homemade 2x4 frame and wedge.
Now to the hydraulic part. A little bottle jack from Harbor Freight less than $20. (I carry this in my car to fix flats too.)
The first bead is easier than the second. I usually have to press against the rim on the opposite side to get it off, but it doesn't hurt anything.
Now the frame holds the wheel to get the tire. This helps when the wheels still have a brake rotor on them,
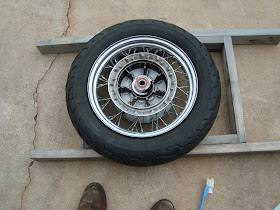
I use three irons. I really like the skinny one with the handle to run point. Then the other two hold things still so the tire doesn't jump back into the rim.

Once the tire is off the side, pull the inner tube out.

Now to the other side. I turn it up and get it started, then rip it off.
Now do the front tire and wheel the same way. Tires are hard work, but you feel like a real man when you're done.